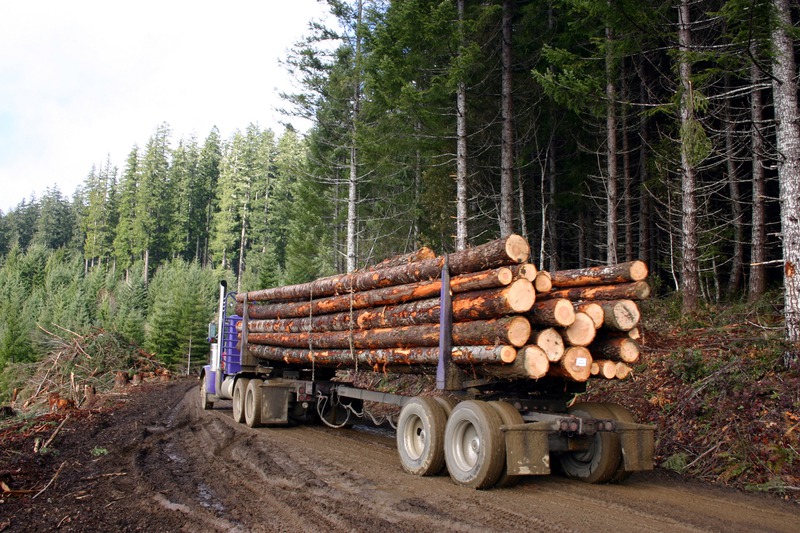
What Factors Affect Logging Costs?
Logging isn’t just about chopping down trees; it’s a complex process involving everything from planning and cutting to transportation and sales. All these steps have associated costs that can fluctuate based on a variety of factors.
1. Equipment and Maintenance
The backbone of any logging operation is its equipment. From feller bunchers to skidders and from log loaders to harvesters, these machines are costly. Purchasing or leasing them comes with a hefty price tag. Maintenance and repairs can also take a big bite out of a logger’s budget, which is why equipment costs are high on the list of what affects logging prices.
Timber cruising informs loggers and landowners alike about the quantity and quality of timber, helping them make informed decisions about harvest and sale. It involves measuring trees, evaluating their condition, and estimating their worth. The detailed information gathered by timber cruising professionals is used to ensure that logging practices and sale agreements are fair and profitable.
2. Labor Costs
Have you ever tried lifting a log? It’s not a one-person job. Logging is labor-intensive and requires a skilled workforce. Paying wages, providing training, and ensuring safety measures are all part of the labor costs, which are essential for a successful operation.
Lane County logging companies face the same cost pressures as others globally—with additional regional twists. Rapid economic changes, fluctuations in regional demand for wood products, and the unique topography of the area all affect the cost structure of logging operations based here.
3. Market Demand and Log Supply
It’s basic economics—the principles of supply and demand play a significant role in logging costs. When there’s a high demand for wood products, log prices usually go up. Likewise, if there’s an oversupply of logs and a market slump, prices will drop. This balancing act is crucial in determining the final logging bill.
In the Pacific Northwest, log marketing plays a crucial role in the logging industry. It’s the art of selling your logs and making sure you’re getting the best bang for your buck. With the help of log marketing Oregon experts, loggers can find buyers and negotiate prices that reflect the true value of their timber. The strategy involves understanding market trends, knowing which wood products are in demand, and having a knack for timing the sales just right.
4. Accessibility and Terrain
The accessibility of logging sites and the terrain characteristics significantly impact operational costs. Sites located in remote or rugged terrain may require additional effort and resources to access, increasing transportation costs and equipment wear and tear. Terrain features such as steep slopes, rocky terrain, or wetlands can pose challenges to logging operations and necessitate specialized equipment and techniques.
5. Transportation and Logistics
Transporting logs from the forest to processing facilities involves logistical challenges and associated costs. Factors such as distance traveled, road conditions, fuel prices, and transport availability influence transportation expenses. Efficient logistics management, including route optimization and coordination of transportation resources, is essential for minimizing costs and ensuring timely delivery of logs to market.
6. Regulatory Fees and Compliance
The logging industry is subject to various regulations aimed at environmental protection, sustainable forest management, and worker safety. Acquiring permits, complying with regulatory requirements, and paying associated fees are essential aspects of conducting logging operations legally and responsibly. Failure to adhere to regulations can result in fines, legal liabilities, and reputational damage for logging companies.
7. Environmental Considerations and Best Practices
Discussion on logging costs would only be complete with mentioning environmental considerations. Adhering to best practices for sustainable logging ensures the forest’s health for generations to come, but it can also add to the overall costs. Measures such as selective cutting, maintaining buffer zones, and ecosystem restoration are all part of this balancing act.
8. Insurance and Risk Management
Like any industry, logging has its risks. Ensuring adequate insurance coverage for personnel, equipment, and potential environmental issues is vital. These costs of doing business securely can also impact the overall financial picture for logging operations.
9. Impact of Technology and Innovation
-
Efficiency Improvements: Advancements in logging technology not only make operations safer, but they can also boost productivity and reduce costs in the long run.
-
Data Management: Software for managing inventories and operations helps optimize the entire logging process, saving time and money.
-
Environmental Tech: Innovations that minimize environmental impact can also reduce the costs associated with regulatory compliance and remediation.
Final Thoughts
We’ve woven our way through the complex tapestry of logging costs, touching on key components like equipment, labor, market dynamics, and a whole host of other factors that intertwine to create the final price tag of wood products. Remember, every choice made by loggers, from the moment they plan a harvest to the second they sell the logs, is guided by these elements. As the forestry and logging industries continue to evolve, keeping an eye on these cost factors will help us understand the ever-changing landscape of wood as a resource.